Your web browser is out of date. Update your browser for more security, speed and the best experience on this site.
How do you treat an odour-laden airflow?
We determine and optimise the best air treatment technology for odour-laden airflow.
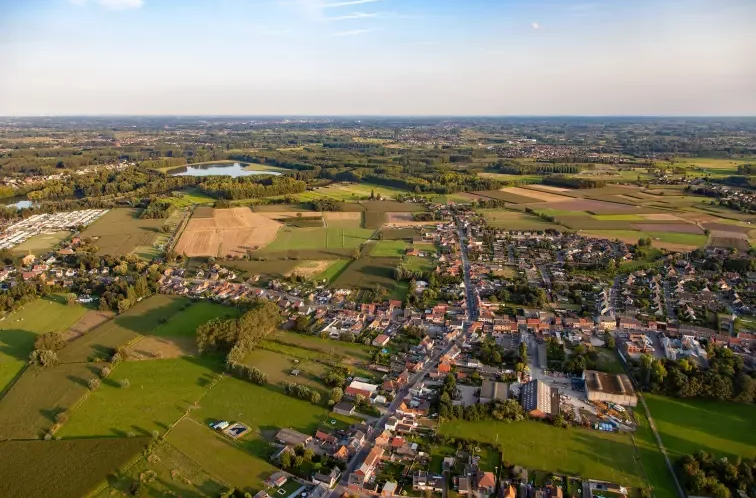
Introduction
Several industrial activities can lead to a negative odour impact on the environment. To minimise this impact, odour-laden airflows are extracted and diverted to odour treatment techniques. The effectiveness of these techniques should be investigated to determine whether the particular technique is adequately suited to treat the odour-laden airflow and/or whether even better alternatives may exist.
OLFASCAN aims to support customers in this regard by providing various pilot setups of odour treatment techniques to investigate, through sampling and analysis, which technique (or combination of these) is preferred for treating specific odour-laden airflows. In this way, the odour impact on the environment can be reduced more efficiently.
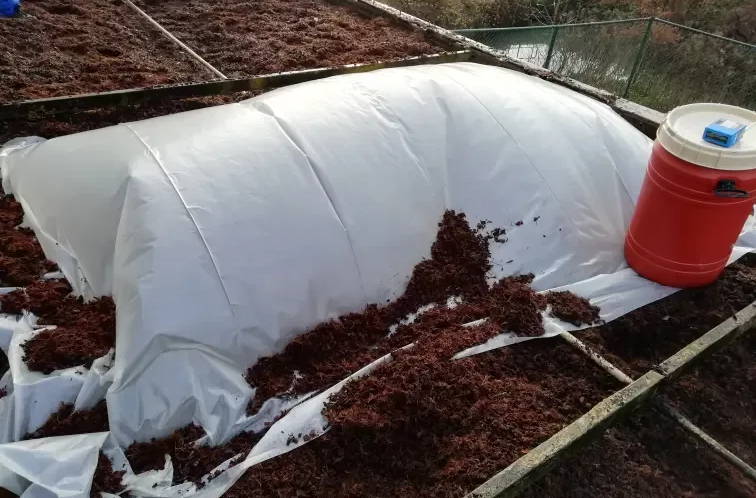
How do you choose an odour treatment technique?
Depending on the type of odour components to be removed, there is a wide range of odour treatment techniques (activated carbon filtration, biofiltering, scrubbing, UV filtration, etc.). Each of these techniques has its advantages and disadvantages for the removal of specific odour components. At several companies with some odour impact on the environment, one of these techniques (or a combination of these) has often already been implemented as a full-scale setup.
The choice of technology here relies on characteristics of the production process, and the possible exemption of odour components from this process. However, a thorough analysis of the odour components formed is often lacking, so the chosen technique may not be sufficiently efficient in removing the odour components.
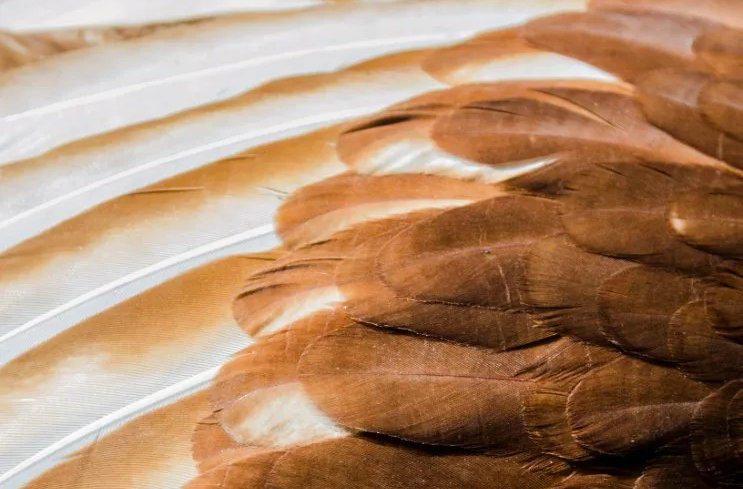
Existing odour treatment proves insufficient for chicken feather meal producer
Chicken feathers contain lots of keratin (protein), which is a significant ingredient in producing high-protein pet food. However, keratin has a rigid structure made up of sulphur bonds. The processing of feathers into a nutrient-rich flour is therefore accompanied by the release of odour components such as organic sulphur compounds, H2S and SO2.
To reduce the odour impact of the process, the exhaust air stream is passed through a slightly acidic scrubber, basic oxidative scrubber, condenser and two serially connected activated carbon filters. So that the airflow after the condenser would not be too moist for the activated carbon filters, an additional dry process flow is added to the activated carbon filters.
Despite the presence of the odour treatment, the producer still periodically receives odour complaints.
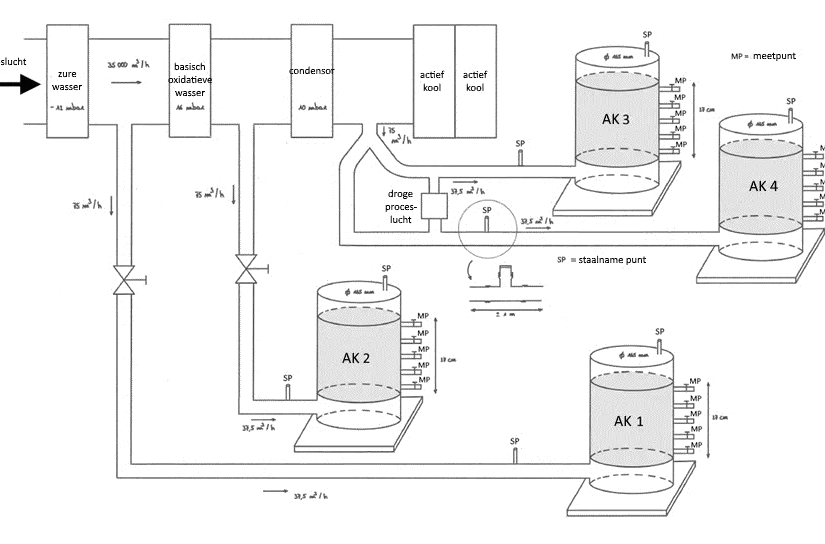
Pilot setups at producer of chicken feather meal
To investigate the efficiency of full-scale odour treatment at the chicken feather meal producer and to ascertain whether there are no better alternatives, activated carbon filter pilots were set up at different stages of odour treatment.
Pilot activated carbon filters 1 and 2 (AK 1 and AK 2) were filled with both impregnated and non-impregnated carbon. Pilot activated carbon filters 3 and 4 (AK 3 and AK 4) were filled with non-impregnated carbon. Air samples were taken weekly at the inlets and outlets of the pilot activated carbon filters (sampling points), which were then analysed for volatile organic compounds (VOC), H2S and SO2. To monitor the adsorption capacity of the carbon, pH measurements were performed on carbon samples taken through the activated carbon filters.
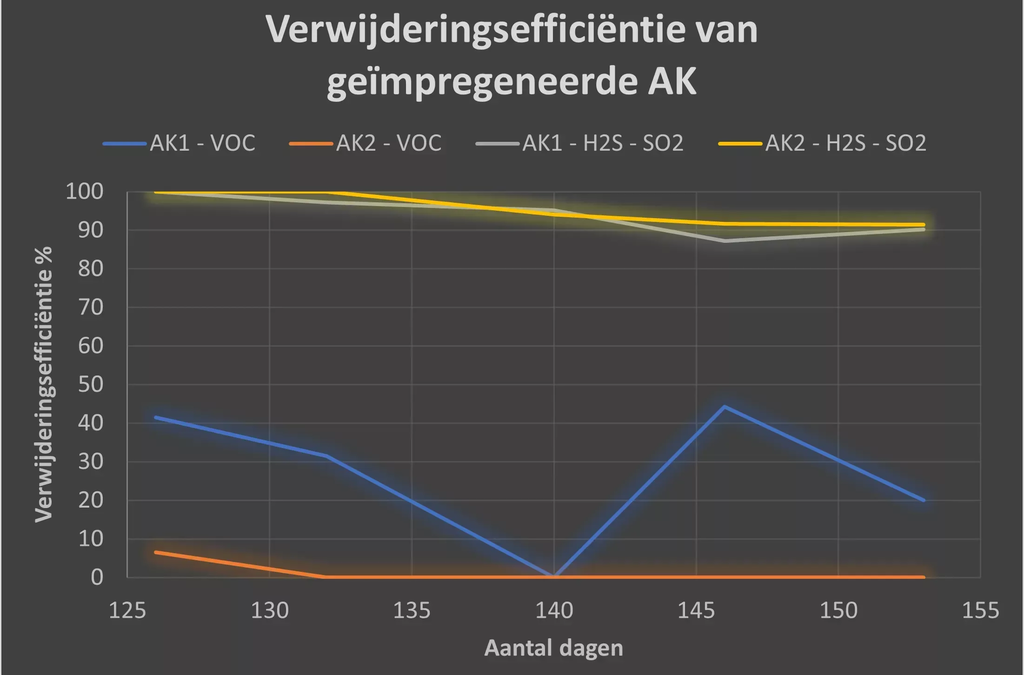
Analysis removal efficiency impregnated AK
When the results of the measurements are evaluated, we see that AK1 and AK2 can efficiently reduce H2S and SO2 over a long period of time. This type of carbon acts as a basic oxidative scrubber, but is more cost-effective and easier to maintain.
However, the removal efficiency of VOC here is very low. A combination of both types will be necessary for obtaining a high reduction of VOC as well as H2S and SO2.
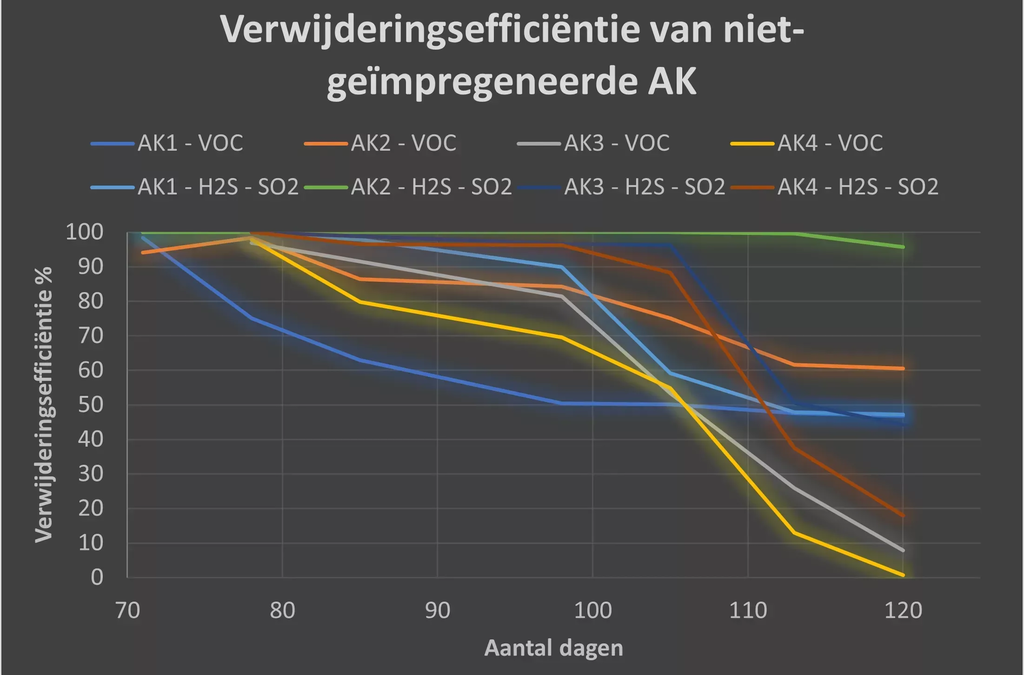
Analysis removal efficiency non-impregnated AK
Non-impregnated carbon is best suited for VOC removal. AK 3 and AK 4 had lower and shorter VOC removal because these pilots were subject to the extra dry process airflow. This flow had been added by the manufacturer to reduce the moisture content toward the carbon filters, but backfired because it was overloaded with VOC, H2S and SO2. Based on this analysis, this flow was therefore shut off.
AK 2 showed the highest and most prolonged VOC, H2S and SO2 removal because this carbon filter was switched after the basic oxidative scrubbing so H2S and SO2 were already efficiently removed.
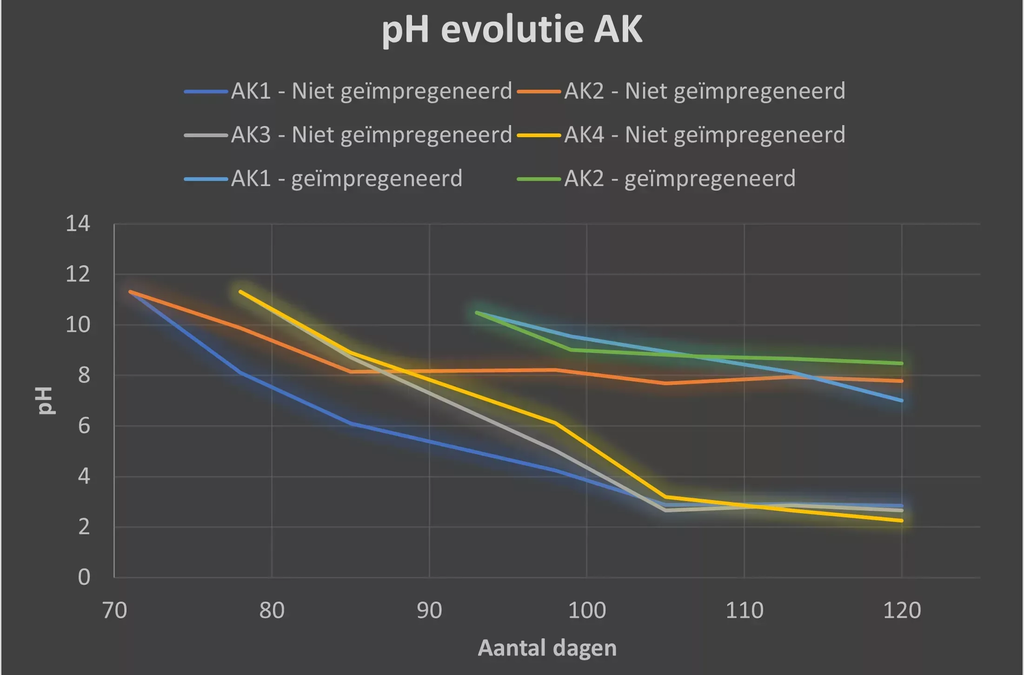
Adsorption capacity analysis
The pH analyses on the pilot activated carbon filters showed that AK 1, AK 3 and AK 4 with unimpregnated carbon exhibited faster acidification than AK 2. This is again attributable to the position because AK 2 receives a reduced H2S/SO2 load due to the prior reduction of these components by the basic oxidative scrubber. The impregnated carbon shows little acidification, which is evidence of its high adsorption capacity for H2S and SO2.
So monitoring pH is a good parameter to monitor the AK's stand time.
Conclusion
Pilot experiments and chemical analysis can be used to investigate the efficiency of existing odour treatment techniques to further optimise them.
For the chicken feather meal producer, it was thus demonstrated that the basic oxidative scrubber could be replaced by a more cost-effective impregnated carbon filter with very high removal efficiency for H2S and SO2. Such pretreatment is necessary to increase the efficiency of VOC removal by downstream non-impregnated carbon.
The pilot setups also showed that the addition of dry process air was detrimental to the VOC removal efficiency of the carbon filters and thus this flow had to be turned off.
Using pH measurements, the adsorption capacity of the carbon filters can also be monitored to better control the replacement rate of the carbon filters.
How can we help?
If you’d like additional information, or have a specific question for one of our staff members, be sure to get in touch through our contact page.